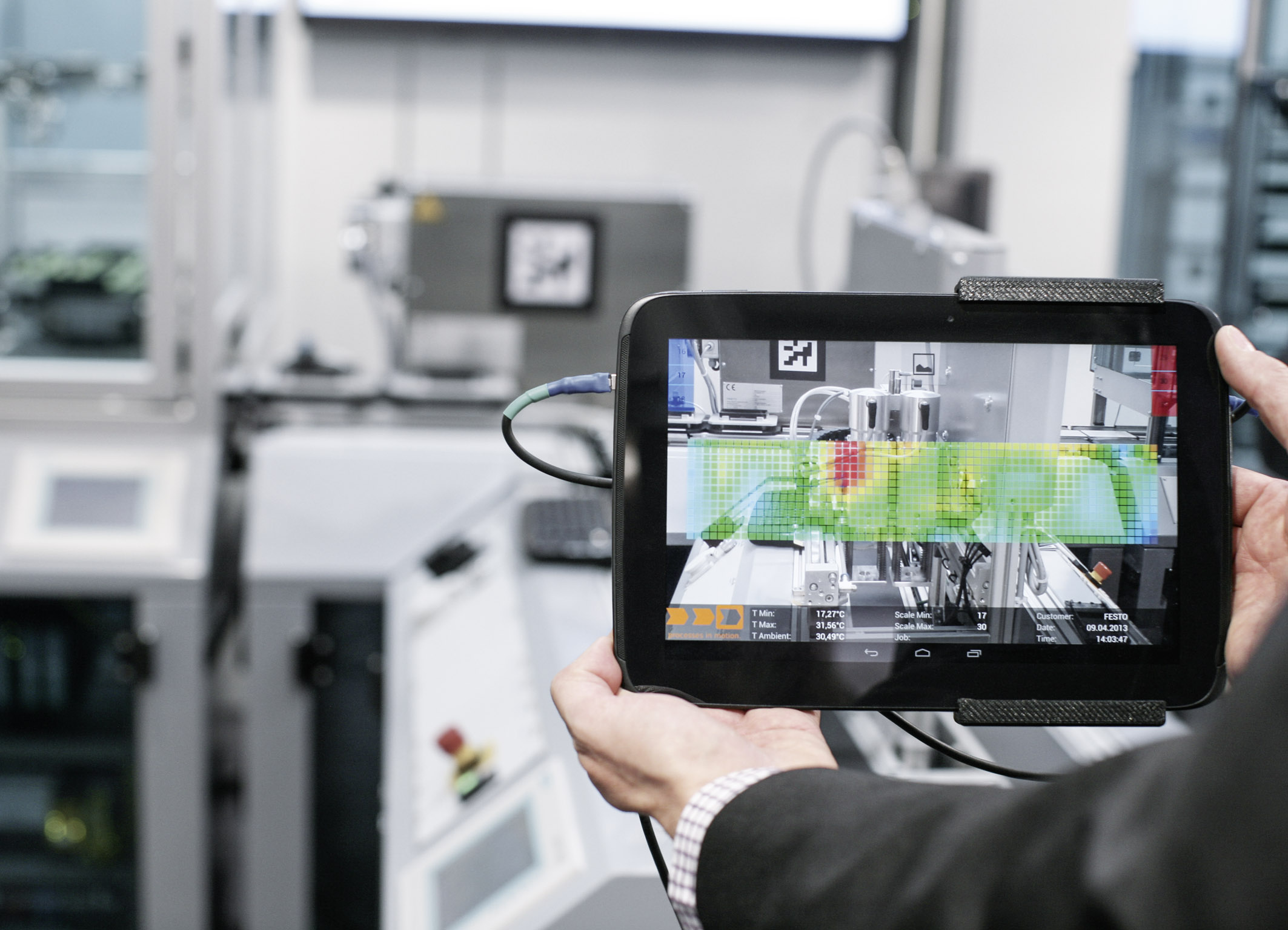
L’industrie manufacturière se trouve, aujourd’hui, sur le seuil d’une quatrième révolution industrielle. L’aube du 3ème millénaire a été marquée par l’émergence progressive des systèmes intelligents et autonomes de production. L’intégration des clients et des parties intéressées dans le processus décisionnel devient un atout concurrentiel pur de nombreuses compagnies industrielles.
Le terme « Industry 4.0 » fait référence à la 4ème révolution industrielle et a été utilisé pour la première fois en 2011, à l’occasion De la foire de Hanovre 2011 (salon de la technologie industrielle).
Dans ce contexte, le gouvernement allemand a initié un projet quasi-futuriste dans le domaine des hautes technologies. Le but de ce projet est d’encourager l’adoption de la notion « d’usine intelligente ». Cette notion repose sur la polyvalence, l’optimisation, l’efficience, la conception ergonomique et l’intégration des clients et des partenaires dans les processus de valeur ajoutée. Les systèmes cyber-physiques et l’internet des objets sont les technologies de base pour cette notion.
Le concept « industry 4.0 » repose sur les éléments suivants :
- La numérisation de l’usine : L’usine intelligente se caractérise par la communication en continu et en temps réel entre les différents agents (machines, convoyeurs, postes de commande, …) intégrés dans le chaînes de production et d’approvisionnement. L’utilisation de capteurs communicants apporte au système la possibilité de faire un autodiagnostic et un auto-réajustement en cas de modifications imprévues survenues au système.
- La flexibilité et la personnalisation de la production : La flexibilité est accrue par l’utilisation d’outils de production intelligents et réadaptables. Le consommateur final, ainsi que les parties intéressées, prennent place dans le processus décisionnel et opérationnel de fabrication.
- Des nouveaux outils logistiques : L‘usine intelligente génère un flux d’informations important qui doit être communiqué aux différents agents intérieurs et extérieurs à l’usine, ceci en temps réel. La technologie RFID se trouve comme élément clé. Elle permet l’identification et la traçabilité des produits à travers le monde entier.
- Des outils de simulation : La base des connaissances générées par les différents agents du système de production permettent de produire des répliques virtuelles du système physique. Ceci permet de générer des simulations pouvant servir comme bancs de tests ou même des outils de conception et de personnalisation au service du client.
- Une usine économe en énergies et efficiente : Le réseau de communication et d’échange instantané entre les différents agents de production permet d’optimiser les processus en temps réel et d’économiser en consommations et en déchets. Ceci permet à la fois de réduire les coûts de production et de répondre aux problématiques actuelles de gestion des ressources et de l’énergie.